Explore more from Uniform and Kit
Wool, wax and whalebone: Preparing a uniform for display
4 minute read
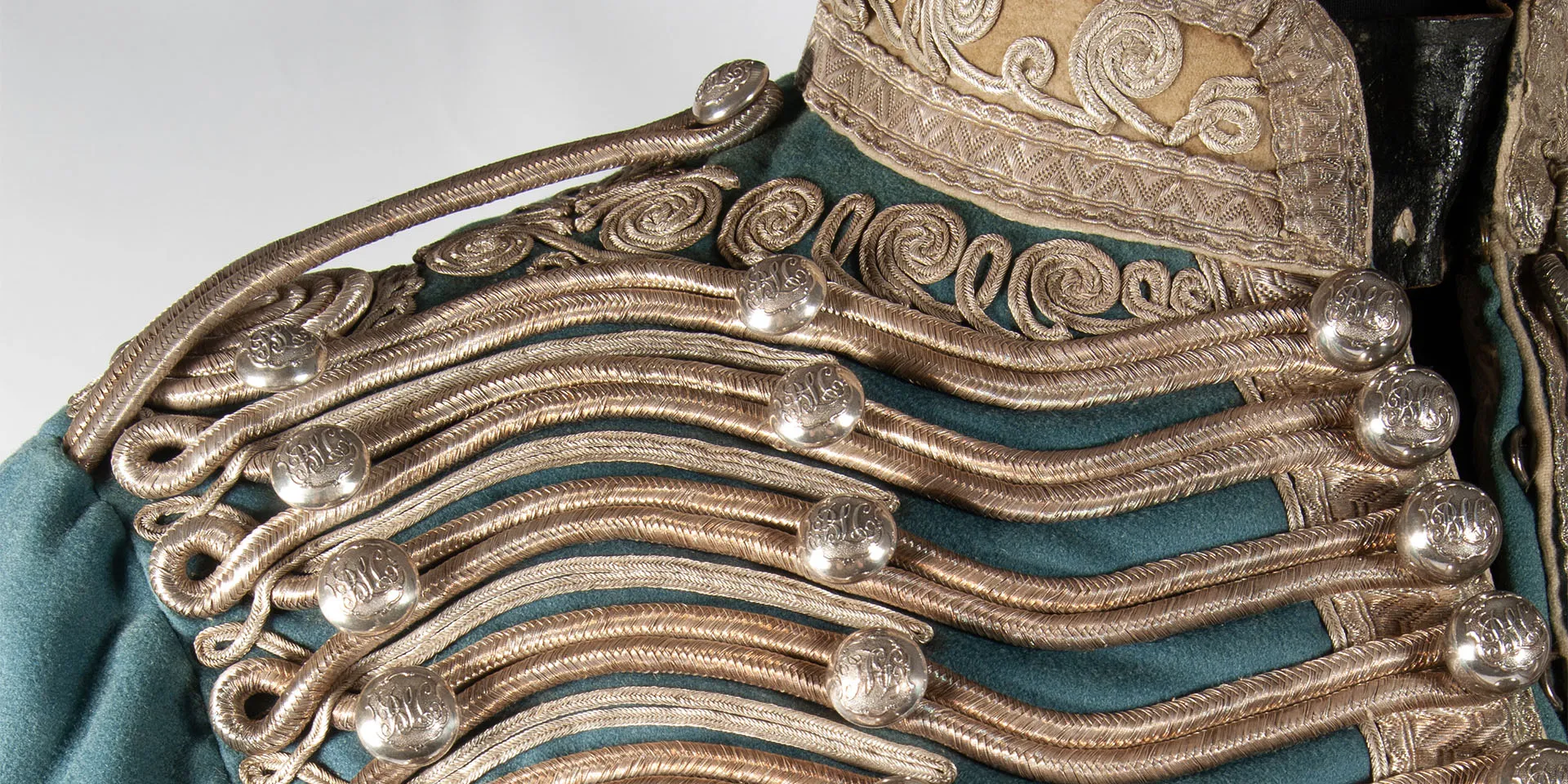
Jacket worn by Captain John Malcolmson VC, c1860
A unique collection
John Grant Malcolmson was a Scottish soldier, who joined the 3rd Bombay Light Cavalry in 1855. He served in several Indian Army campaigns and was awarded a Victoria Cross (VC) for his actions in the Persian War of 1857.
His uniform and medals form part of a unique collection gifted to the National Army Museum by one of his descendants. This collection also includes a full-length portrait of Malcolmson, which is currently on display in the Indian Army Memorial Room at the Royal Military Academy Sandhurst.
Care and attention
Before items like this can go on display, we undertake an initial assessment to estimate how much treatment is needed. We factor in time for materials testing and other specific tasks, such as testing different conservation dyes or adhesives.
Altogether, the Malcolmson Collection needed over 100 hours of treatment - the jacket, helmet and plume requiring the most significant intervention. The jacket alone received almost a month’s worth of practical work.
The oil painting was very helpful throughout the conservation process. It's extremely rare to have such a direct point of reference for objects or uniforms as unusual as these.
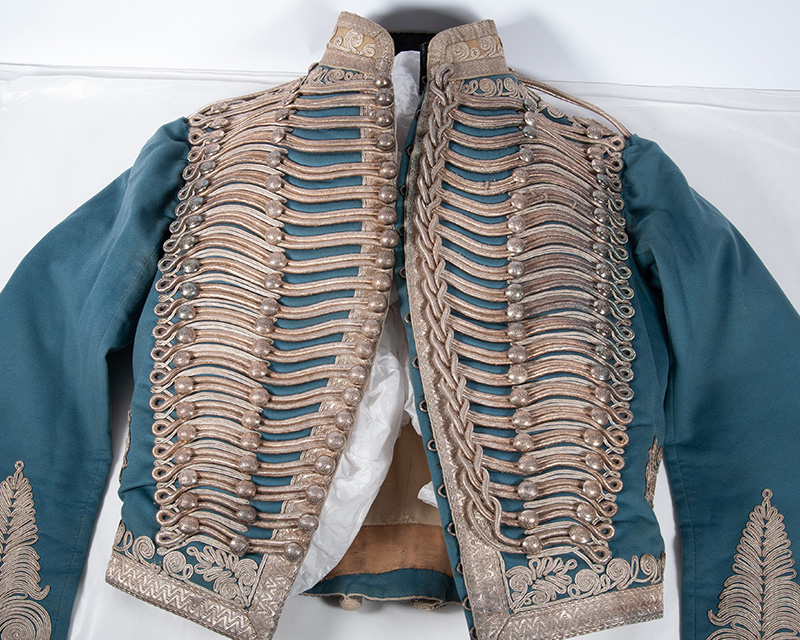
The condition of the jacket before treatment
Jacket
The uniform jacket is made of light blue wool, with silver buttons and silver-plated lace frogging. The inner silk lining was in a poor condition and threadbare in many places. The silk was probably weighted to add to its value, which unfortunately accelerated the deterioration.
To prepare the jacket for display, we had to support the silk weave. We used dyed colour-matched silk crepeline fabric coated with conservation-grade adhesive and some stitching. The stitching used extremely fine curved needles, less than 1mm thick.
Although most people will never see the lining, this work was essential to make the jacket structurally stable enough to display on a mannequin, without risking further loss to the material.
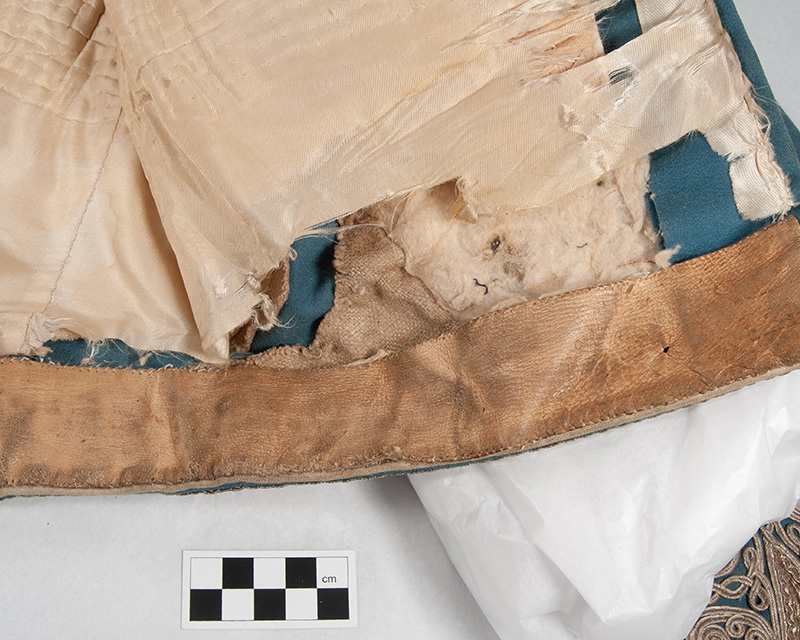
The jacket's inner lining before treatment
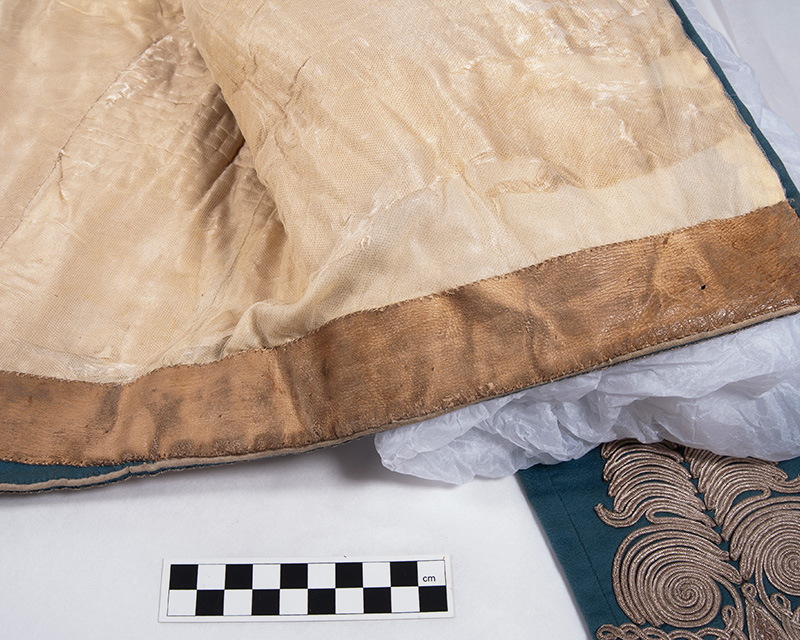
The inner lining after treatment
Buttons
The buttons on the outside of the jacket are silver (or possibly silver-plated). The initial assessment revealed that a reaction had occurred with the wool fabric, resulting in a slight blueish tint.
After a light, surface cleaning, the buttons appeared significantly brighter and more uniform in appearance. We were careful not to over-clean and risk damaging the silver.
In order to display the uniform ‘as worn’ and as it looks in the painting, a tiny strip of silk was inserted between the belt and the jacket. While invisible to visitors, this should protect against some re-tarnishing.
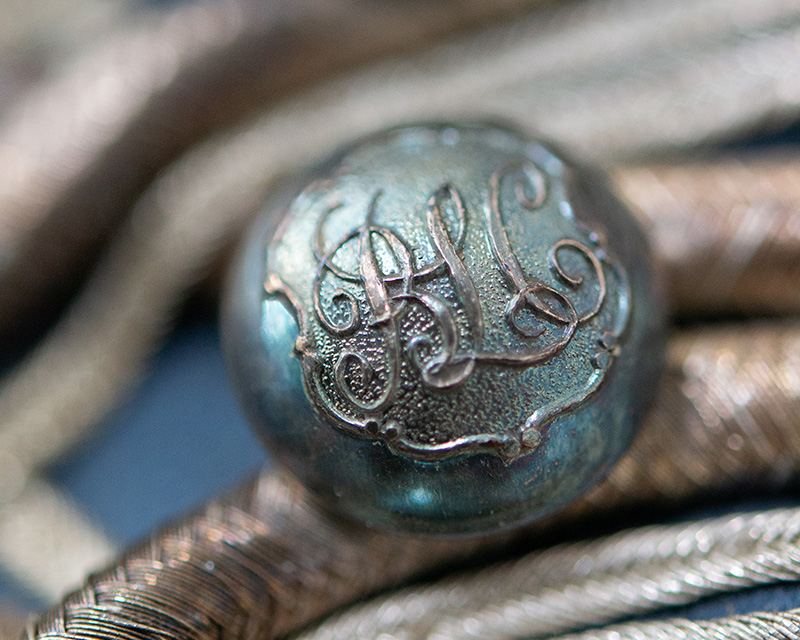
The blueish tint on the jacket's buttons
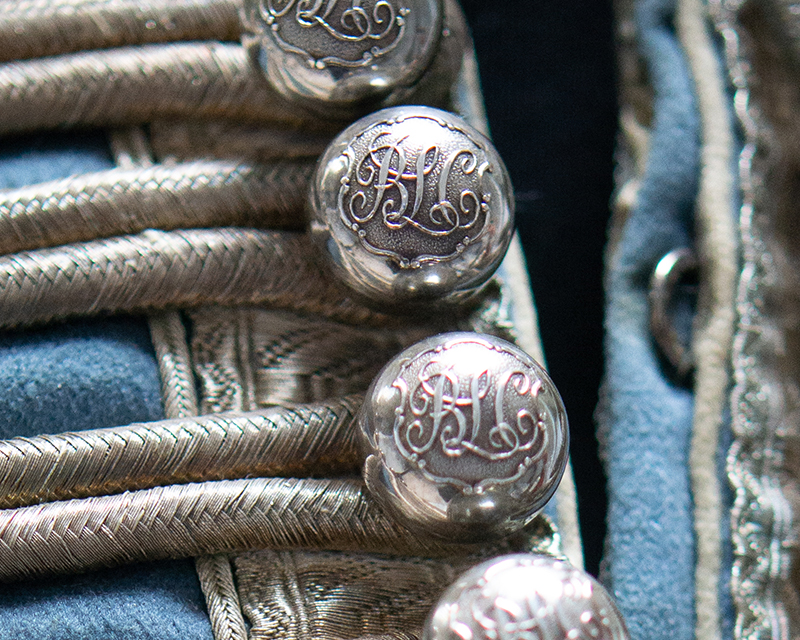
The buttons after some light, surface cleaning
Helmet
The helmet is ferrous, with copper alloy badges and chain. Based on the initial assessment, the exterior appeared to have been regularly polished, but the rose bosses holding the chain at the sides needed work. The textile and leather lining supporting the chinstrap survived only in small fragments.
The metal required solvent cleaning to remove the residues of the polish. We then added a protective coating with conservation-grade wax to reduce future deterioration. This step is vital for preserving metal weapons or armour.
Metals, leather and textiles all need different approaches, so it can be incredibly useful to treat each material individually to preserve their longevity and structural integrity before they go on display. Fortunately, the rose bosses and the plume were detachable, which meant they could be worked on as separate pieces.
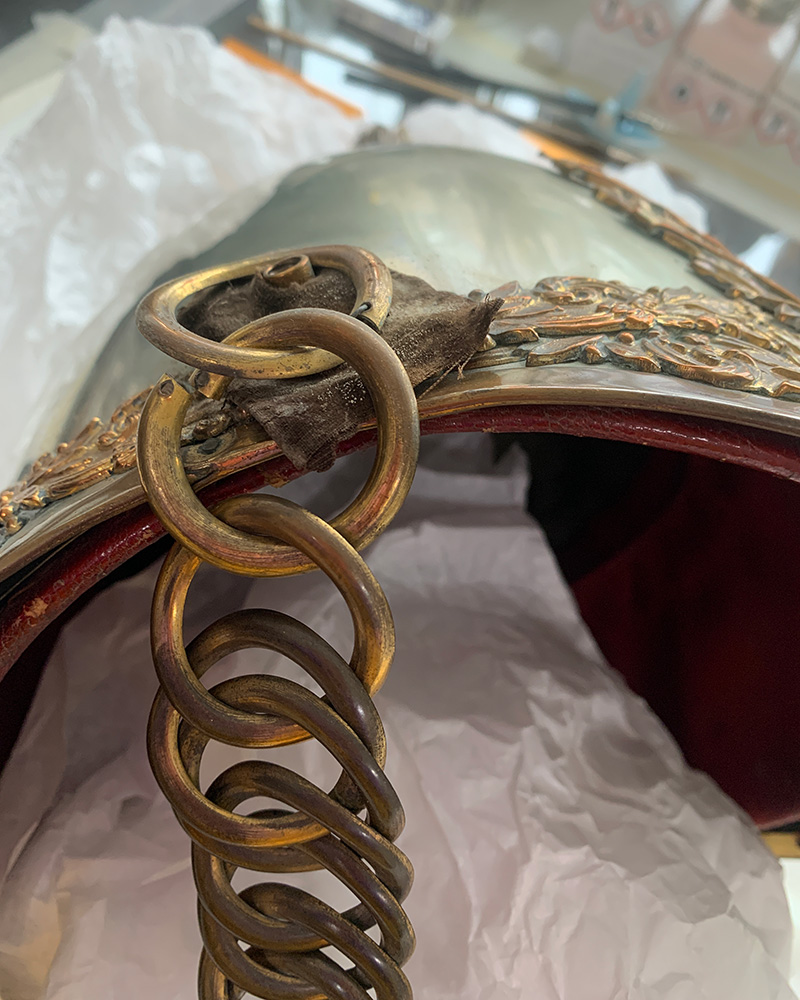
The lining beneath the rose boss before treatment
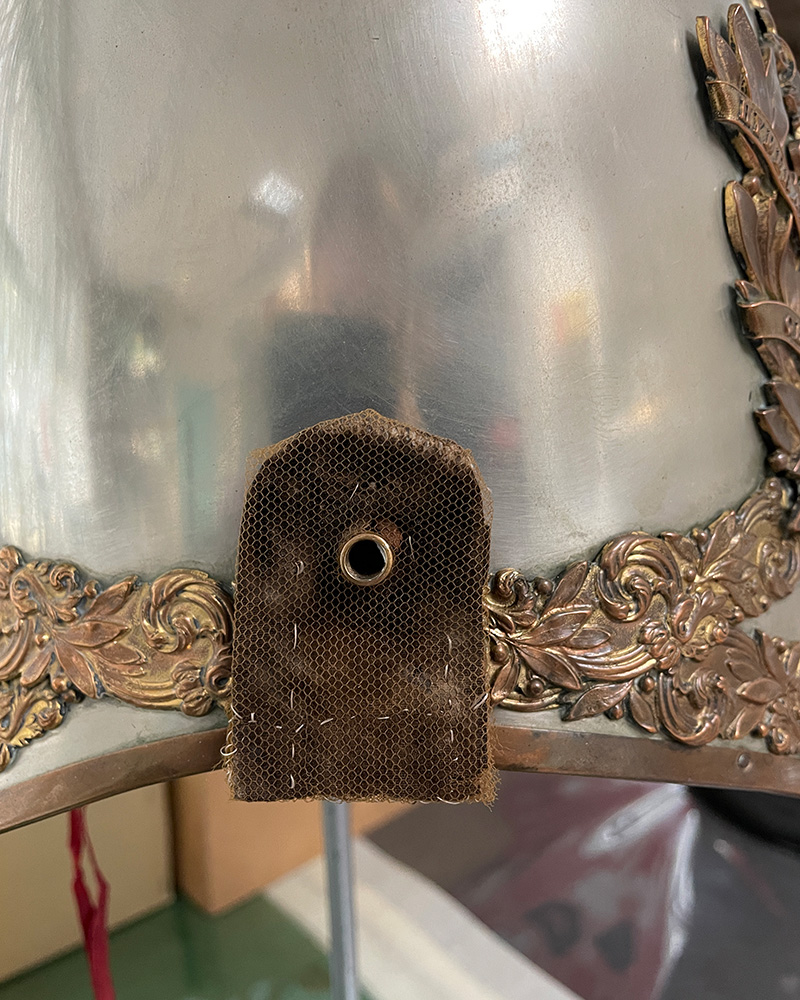
The lining in much better condition after treatment
Plume
The plume needed specialist repairs. We were able to remove it from the helmet and take it apart with help and guidance from Louis Chalmers, one of the few people in the country (if not the world) who can make authentic military plumes. This confirmed for us that it was held together with whalebone, a material traditionally used for its light weight, flexibility and strength.
The bone was in such poor condition that it had to be replaced. However, we were careful to keep the original piece to preserve that part of the object’s history.
Louis also showed us how to reattach the plume to the helmet and shape it using humidification, a process that felt a bit like hairdressing!
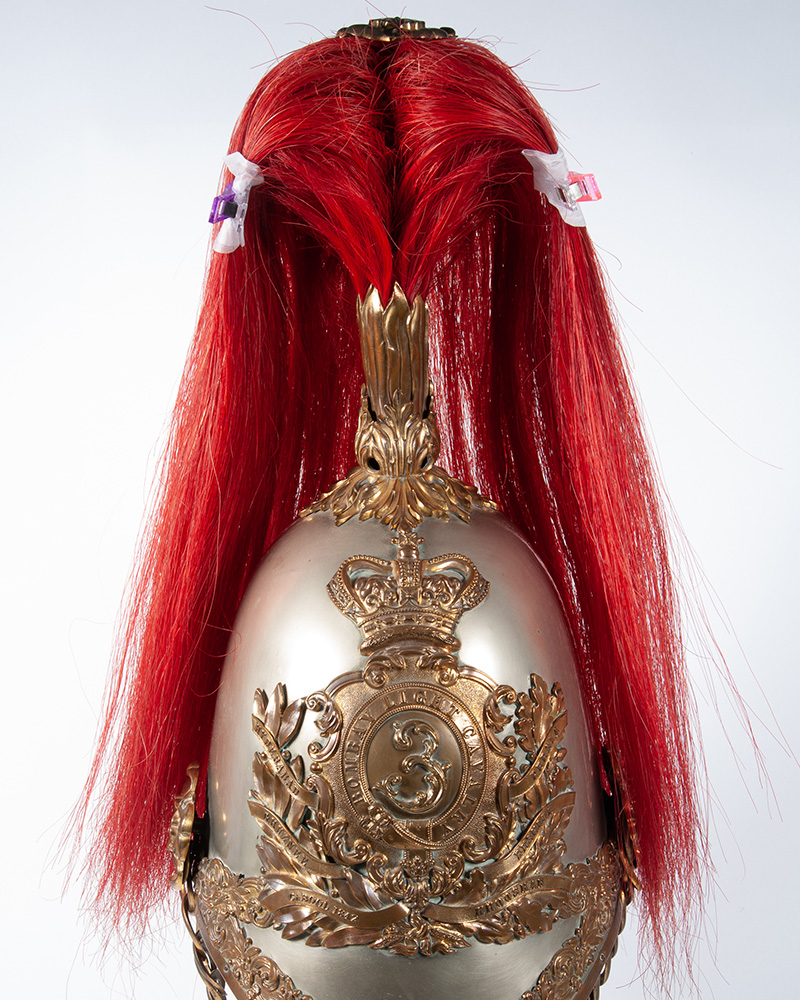
Fitting the repaired plume after treatment (front view)
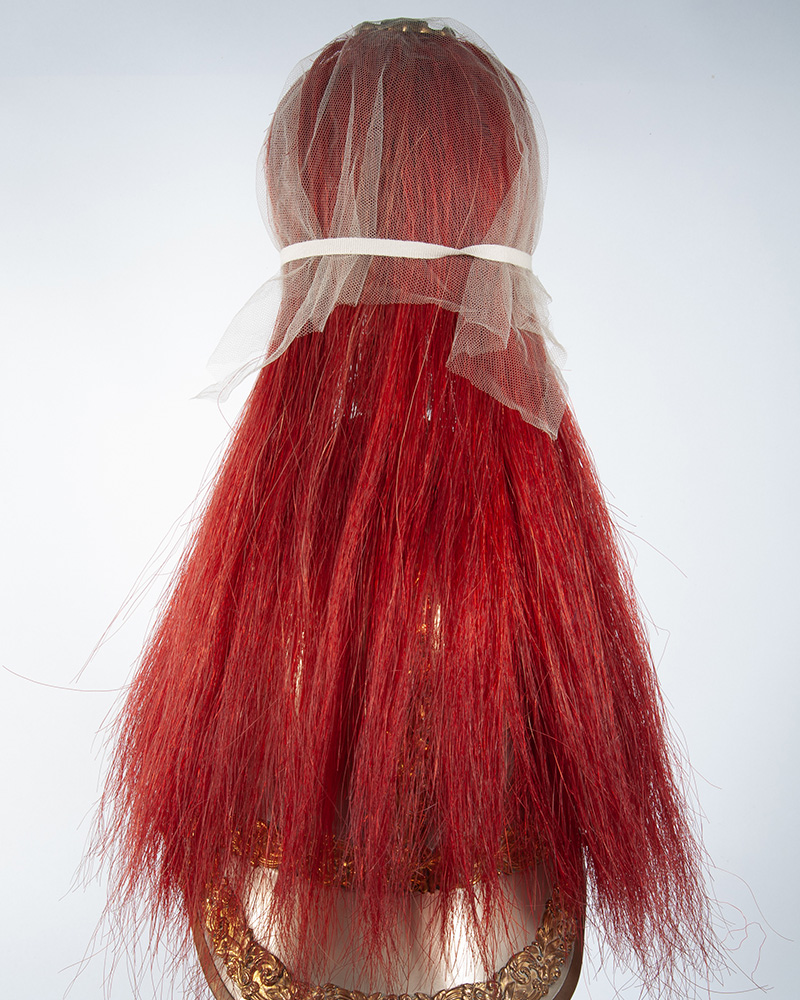
Fitting the repaired plume after treatment (rear view)
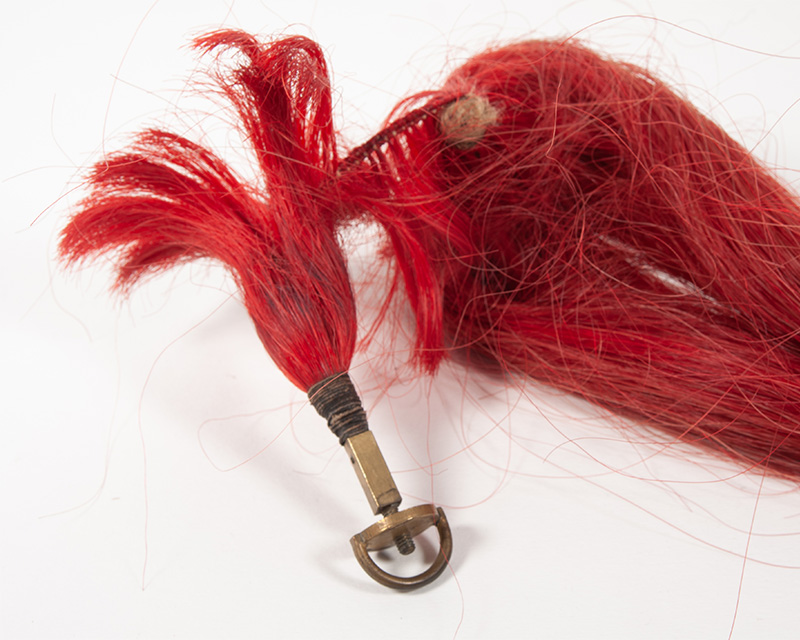
The damaged plume before treatment
See it on display
We're very proud that these unique items have been returned to a condition that will allow future generations to enjoy them for years to come.
The uniform is now on display to the public for the first time, arranged ‘as worn’ along with the Victoria Cross medal group. Come and see them in our Global Role gallery.